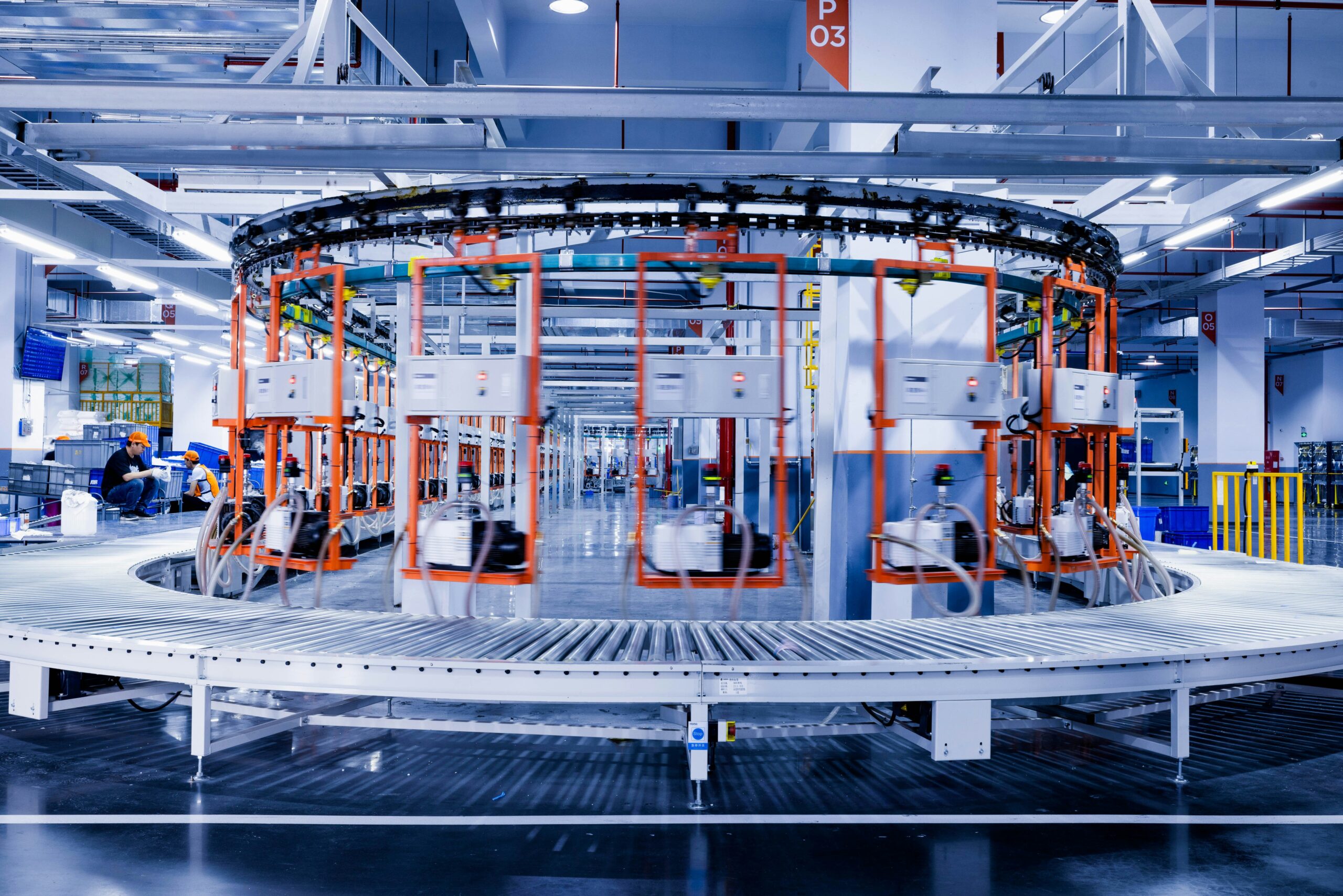
The global manufacturing landscape is evolving, with an increasing emphasis on sustainability as companies seek to reduce their environmental impact. With growing awareness of climate change and resource depletion, manufacturers are under increasing pressure to adopt sustainable practices that are both environmentally and economically responsible. Sustainability in manufacturing is no longer an optional practice—it has become a vital part of a company’s overall strategy for long-term success. From reducing waste and energy consumption to using sustainable materials, manufacturers embrace innovative solutions to minimize their ecological footprint while maintaining operational efficiency.
Optimizing Resource Use and Reducing Waste
One of the primary focuses of sustainable manufacturing is reducing waste. Manufacturing processes traditionally generate large amounts of garbage through excessive materials, packaging, or energy consumption. To minimize waste, manufacturers are adopting Lean practices that focus on continuous improvement, cutting inefficiencies, and eliminating non-value-added activities. This not only reduces environmental harm but also helps companies cut costs.
Another significant practice for reducing waste is improving the efficiency of resource usage. For instance, manufacturers are increasingly adopting methods like Just-in-Time (JIT) inventory management to minimize overproduction and reduce excess materials. Advanced technologies such as automation and artificial intelligence (AI) also play a critical role in waste reduction by improving production precision and helping forecast demand more accurately. These innovations help companies reduce waste and costs while promoting a more sustainable approach to production.
Enhancing Energy Efficiency in Manufacturing
Energy consumption is a significant concern in manufacturing, as factories and production plants consume vast energy, contributing to a larger carbon footprint. To address this challenge, many manufacturers are turning to energy-efficient solutions to minimize their environmental impact while improving their bottom line. The first step in energy efficiency is often an audit of energy use within the factory.
One of the most effective ways to enhance energy efficiency is by adopting renewable energy sources. Solar panels, wind turbines, and geothermal energy systems are becoming more common in manufacturing facilities, providing a cleaner and more sustainable alternative to traditional fossil fuels. In addition, manufacturers are increasingly investing in intelligent energy management systems that use sensors and real-time data to monitor energy usage and adjust operations accordingly. For example, adjusting heating, ventilation, and air conditioning (HVAC) systems based on occupancy or production needs can significantly reduce energy waste. These measures reduce operational costs and demonstrate a company’s commitment to sustainability.
Sustainable Material Sourcing and Supply Chain Management
The materials used in manufacturing significantly impact the environment, mainly when those materials are non-renewable or require extensive processing. To drive sustainability in manufacturing, companies are shifting toward sustainable materials with less environmental impact. For example, bioplastics, recycled metals, and natural fibers are gaining popularity as alternatives to traditional petroleum-based plastics and other non-renewable materials.
In addition to sustainable materials, manufacturers are increasingly focused on creating more sustainable supply chains. This involves sourcing raw materials from suppliers who adhere to environmental and social responsibility standards. Transparency and traceability in the supply chain are crucial components of this process. By ensuring that suppliers follow sustainable practices, manufacturers can reduce the overall environmental impact of their products and make more sustainable choices in production.
Manufacturers are also adopting circular economy principles in their supply chains. This model emphasizes reusing, recycling, or refurbishing materials and products, reducing the demand for virgin resources and minimizing waste. For example, companies in the electronics sector are designing products with components that can be easily disassembled and recycled at the end of their life cycle. By embracing circular economy practices, manufacturers can contribute to a more sustainable world while maintaining the quality and performance of their products.
Sustainable Product Design and Innovation
Sustainability in manufacturing doesn’t just happen in the production process—it starts with product design. Designing products with sustainability in mind can profoundly impact the manufacturing process’s environmental footprint. Designers are increasingly focused on creating durable, repairable, and recyclable products. This approach helps to extend the product life cycle and ensures that products can be reused or recycled once they are no longer in use.
Design for sustainability (DFS) encourages manufacturers to reduce the number of components in products, making them easier to disassemble and recycle. Additionally, companies are using sustainable materials such as biodegradable plastics or reclaimed metals, which are less harmful to the environment than traditional materials. Through innovation, companies find new ways to create products that meet consumer demands and have minimal environmental impact.
Furthermore, sustainable product design promotes energy efficiency during product use. For instance, in the automotive industry, manufacturers are designing vehicles with lighter bodies, more efficient engines, and alternative energy sources, such as electric batteries. These innovations reduce the overall energy consumption and emissions during the product’s use, aligning with global efforts to combat climate change.
Adopting Industry-Wide Standards for Sustainability
Sustainability in manufacturing is not just an internal effort; it is a collective challenge that requires industry-wide collaboration. Companies increasingly align their practices with global sustainability standards and certifications, such as ISO 14001 (Environmental Management Systems) and the Global Reporting Initiative (GRI). These frameworks help organizations set measurable environmental goals, track progress, and demonstrate their commitment to sustainability to stakeholders.
Industry collaboration is also key to driving sustainability forward. Manufacturers are working with suppliers, regulators, and other industry leaders to create more sustainable practices across the supply chain. By sharing best practices and setting common standards, the manufacturing sector can collectively reduce its environmental impact and promote sustainability on a global scale.
Sustainability in modern manufacturing is no longer just an option—it is a necessity. Manufacturers can significantly reduce their environmental impact while enhancing operational efficiency by embracing practices that focus on waste reduction, energy efficiency, sustainable material sourcing, and responsible product design. Furthermore, manufacturers can create a more sustainable supply chain and product life cycle by adopting circular economy principles and aligning with global sustainability standards. As consumers and regulatory bodies increasingly demand more sustainable practices, manufacturers prioritizing sustainability will contribute to the planet’s health and position themselves for long-term success in a rapidly changing world. Sustainable practices are now an integral part of modern manufacturing, and those who innovate in this space will lead the way toward a greener, more sustainable future.