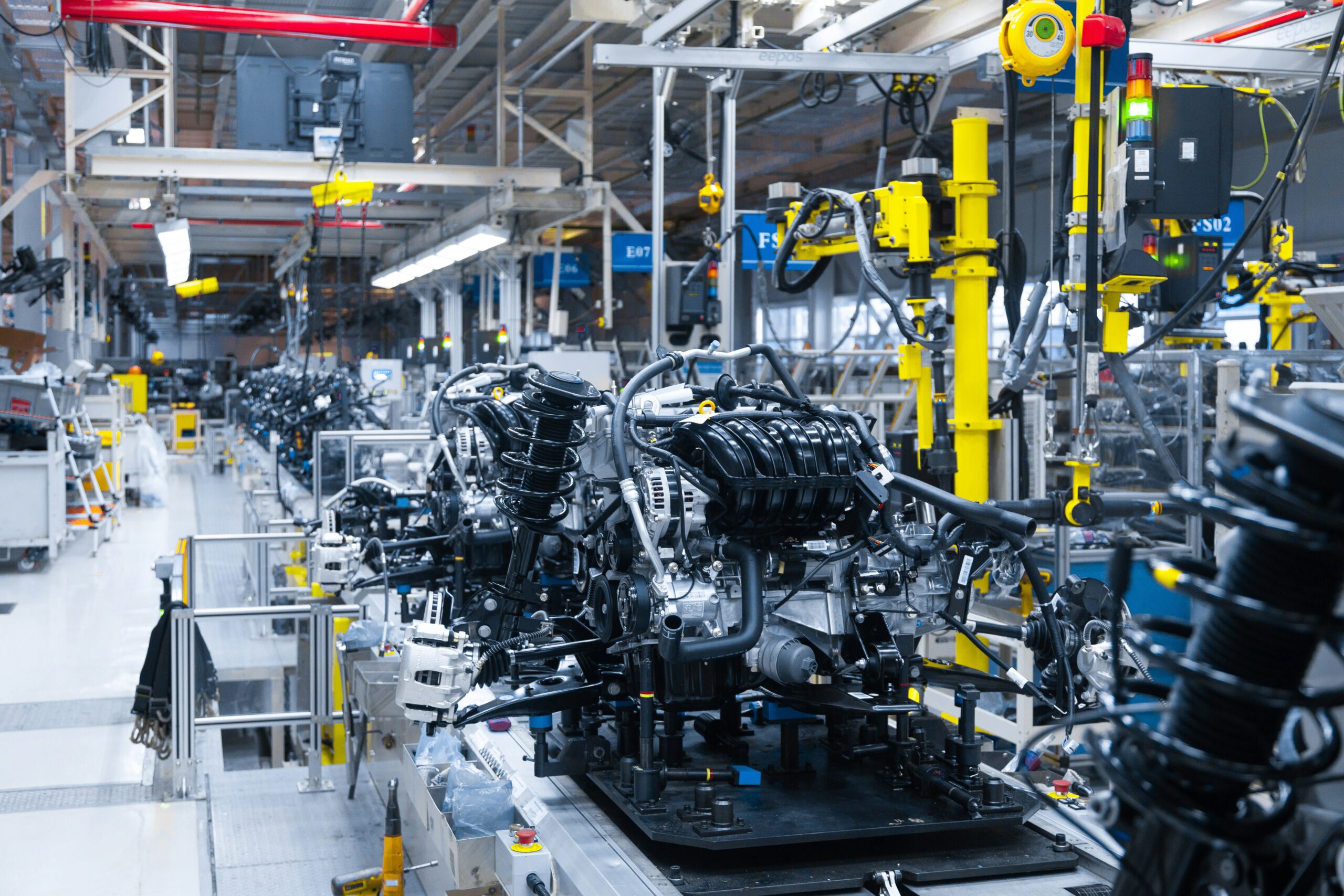
The manufacturing industry is undergoing a dramatic transformation driven by the continuous evolution of technology. Over the past decade, robotics, automation, and data analytics have revolutionized the way factories operate. But what lies ahead? The next wave of innovation promises even more profound changes, with emerging trends set to redefine the way goods are produced and delivered. From smart factories to sustainable solutions, the future of manufacturing technology is both exciting and full of potential.
The Rise of Smart Factories
One of the most significant trends in manufacturing is the development of smart factories. These next-generation facilities use a combination of artificial intelligence, machine learning, and real-time data analytics to optimize production. In a smart factory, machines can communicate with each other, predict maintenance needs, and even make decisions without human intervention. This results in increased efficiency, reduced downtime, and improved product quality.
Smart factories also offer flexibility, enabling manufacturers to adapt to changing demands quickly. For instance, if there is a sudden spike in demand for a particular product, an innovative system can reallocate resources and adjust workflows to meet the need without delay. As this technology becomes more widespread, we can expect traditional factories to evolve into dynamic, intelligent environments.
Additive Manufacturing Going Mainstream
Additive manufacturing, commonly known as 3D printing, is no longer a niche technology; it has become a mainstream technology. While initially used for prototyping and small-scale production, it is now poised to enter mainstream manufacturing. With advances in materials and printing speed, additive manufacturing enables the production of complex components with high precision and minimal waste.
This trend is particularly significant in industries such as aerospace, healthcare, and automotive, where customization and lightweight materials are crucial. In the future, we may see localized manufacturing hubs where 3D printers produce products on demand, eliminating the need for extensive inventories and long-distance shipping. This could lead to a more agile and sustainable manufacturing model.
Sustainability as a Core Focus
Environmental concerns are pushing manufacturers to adopt greener practices, and technology is playing a key role in this shift. Future manufacturing technologies are being designed with sustainability in mind, from energy-efficient machines to closed-loop recycling systems. Companies are investing in clean energy sources, such as solar and wind, to power their facilities and reduce their carbon footprint.
Moreover, digital tools help monitor energy usage and track emissions, enabling manufacturers to make informed decisions that benefit both the planet and their bottom line. In the coming years, sustainability won’t be just a goal—it will be an essential part of every manufacturing strategy.
The Role of Artificial Intelligence
Artificial intelligence is becoming a driving force in manufacturing innovation. AI can analyze vast amounts of data to identify patterns, optimize processes, and predict potential issues before they arise. For example, predictive maintenance powered by AI helps manufacturers avoid costly breakdowns by alerting them to early signs of machine failure.
AI is also transforming quality control. Traditional methods often rely on human inspection, which can be time-consuming and prone to error. AI-enabled vision systems can inspect products in real time with incredible accuracy, ensuring consistent quality and reducing waste.
As AI continues to evolve, it will become an indispensable tool across all stages of the manufacturing process, from design to distribution.
Human and Machine Collaboration
Despite the growing presence of automation, humans will continue to be an essential part of the manufacturing process. The future lies in collaboration between people and machines. Cobots, or collaborative robots, are designed to work alongside humans, enhancing productivity without replacing workers.
These machines can handle repetitive or dangerous tasks, freeing up employees to focus on more complex or creative work. By combining human intelligence with machine efficiency, manufacturers can create a more balanced and adaptive workplace.
Training and reskilling will be crucial as new technologies emerge. Workers will need to understand and interact with advanced systems, which means education and workforce development must keep pace with innovation.
Digital Twins and Virtual Manufacturing
Another trend gaining momentum is the use of digital twins—virtual replicas of physical systems. These models allow manufacturers to simulate, test, and optimize processes before implementing them in the real world. This reduces the risk of errors, lowers costs, and accelerates innovation.
Digital twins can also be used for training purposes, providing workers with a safe and realistic environment in which to learn new skills. In the future, entire production lines may be managed through virtual platforms, enabling remote monitoring and rapid adjustments to operations.
Looking Ahead
A blend of innovation, connectivity, and sustainability is shaping the future of manufacturing. As technology continues to evolve, it will present new opportunities and challenges for businesses worldwide. Embracing these trends will not only enhance efficiency but also position manufacturers to compete effectively in an increasingly digital and environmentally conscious world.
From smart factories and AI to 3D printing and digital twins, the next big thing in manufacturing is already on the horizon. The key to success lies in adaptability—those who invest in future-ready technologies today will be the leaders of tomorrow’s manufacturing landscape.