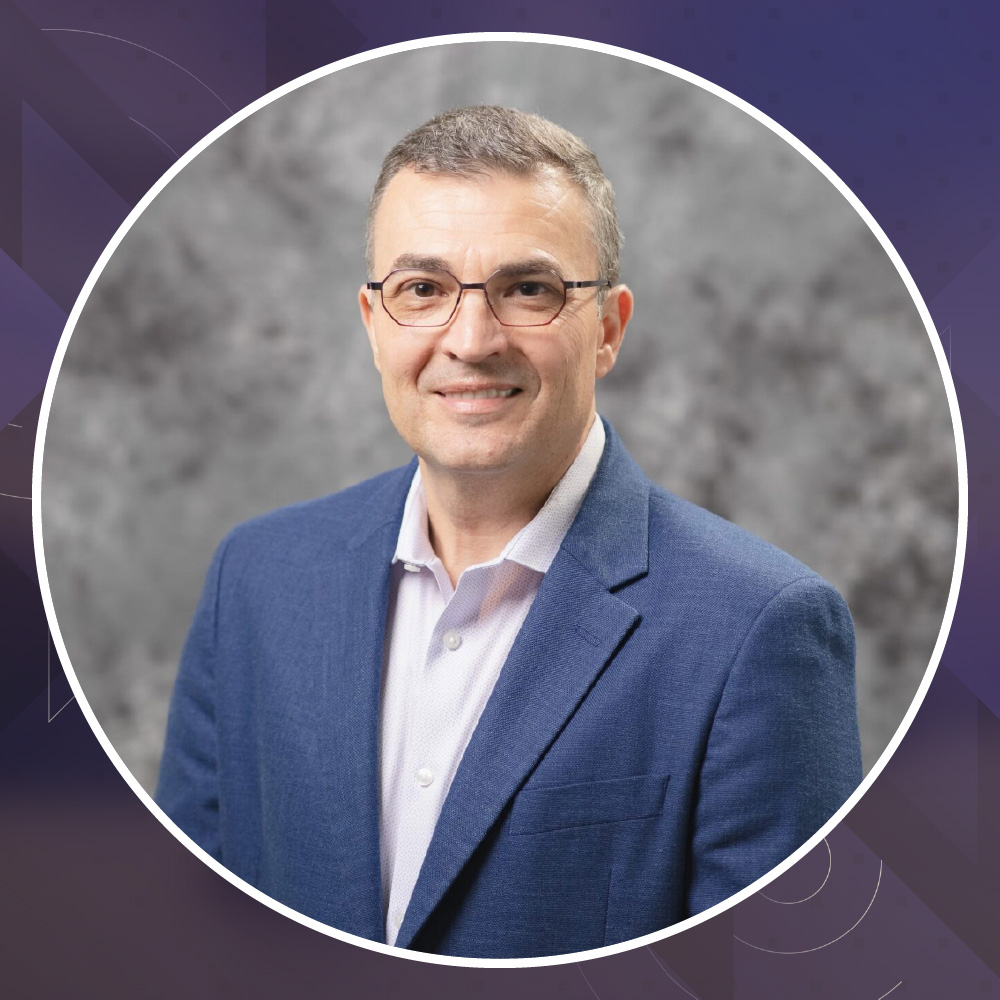
The era of smart factories has dawned, revolutionizing automated production. These highly digitized factories are powered by interconnected systems, advanced robotics, and artificial intelligence (AI), creating a more efficient, adaptable, and data-driven manufacturing environment. As businesses look to stay competitive, the smart factory model is increasingly becoming the standard for optimized production.
What Defines a Smart Factory?
A smart factory stands out by its capacity to integrate digital technologies, allowing machines, systems, and people to communicate and collaborate seamlessly. Smart factories can collect and analyze data in real-time using sensors, AI, and machine learning, providing insights that drive immediate decision-making. This integration helps manufacturers anticipate issues, optimize workflows, and ensure resources are efficiently used.
Not only do smart factories enable continuous improvements, but they also offer the flexibility that traditional factories lack. For instance, smart factories can quickly adapt to changes in production demands without sacrificing efficiency or quality. This adaptability is crucial in a marketplace where customer needs and trends evolve rapidly. As a result, businesses equipped with smart factories can innovate and pivot faster, giving them a significant edge.
Increased Efficiency Through Automation
One of the most immediate benefits of a smart factory is the substantial boost in efficiency through automation. Automation reduces the need for manual intervention in repetitive or complex tasks, which speeds up production and minimizes the risk of human error. For example, automated machines can handle tasks like quality control, packaging, and even maintenance, all while running continuously. Consequently, the production cycle becomes faster, and workers can focus on more strategic roles.
Furthermore, integrating AI into these automated systems enhances efficiency by predicting and preventing potential issues. For instance, predictive maintenance uses AI to analyze patterns in machine performance, identifying when a machine might require repairs before a breakdown occurs. This proactive approach avoids costly downtime and extends the lifespan of equipment. Combining AI-driven automation and predictive maintenance ultimately results in a leaner, more efficient manufacturing operation.
Real-Time Data for Informed Decision-Making
In a smart factory, data flows freely between connected devices, providing real-time insights that support swift, informed decision-making. This data-driven approach allows manufacturers to respond to production challenges rather than relying on retrospective analyses. With sensors collecting and transmitting data across every stage of the production process, managers can monitor key performance indicators (KPIs) in real-time. Thus, they can make adjustments to optimize productivity and address any bottlenecks.
Additionally, real-time data enables manufacturers to track inventory levels accurately, reducing the risk of overproduction or shortages. Companies can avoid unnecessary costs associated with excess stock or missed demand by knowing exactly when to order materials or adjust production. Moreover, with access to detailed data, companies can continuously refine their processes, leading to long-term improvements in quality and efficiency. Real-time data thus acts as the backbone of a responsive, adaptable production system.
Enhanced Flexibility and Customization
Smart factories offer an unmatched level of flexibility, allowing for greater customization in production. With traditional manufacturing setups, customization often requires manual adjustments, which can be time-consuming and costly. However, smart factories use advanced algorithms and modular designs to adjust production based on demand, enabling rapid shifts between product variants or even different product lines. This capability is especially valuable in electronics and automotive manufacturing industries, where consumer preferences frequently change.
Moreover, the flexibility of smart factories extends to workforce management as well. By automating repetitive tasks, manufacturers can allocate human resources more effectively, placing workers in roles that require problem-solving and creativity. This shift boosts morale and enhances productivity, as employees are less burdened by monotonous tasks. Furthermore, quickly pivoting production allows companies to experiment with limited editions or customized products, meeting consumer demands for unique, personalized options.
Another aspect of flexibility is the ease with which smart factories can scale operations up or down. This adaptability is particularly useful in handling seasonal demand spikes or unexpected market shifts. Manufacturers can meet changing production volumes by reprogramming machines and reconfiguring workflows without a lengthy transition period. Consequently, smart factories enable businesses to remain resilient in fluctuating market conditions.
Improved Sustainability Practices
Sustainability has become a priority in modern manufacturing, and smart factories are well-positioned to contribute to environmental goals. Smart factories utilize data-driven insights to optimize energy consumption, reducing the environmental impact of production. For example, energy management systems track real-time usage across the factory floor, helping to identify areas where energy use can be minimized. In this way, smart factories actively reduce waste and improve resource efficiency.
Additionally, a smart factory setting enhances the ability to monitor and control waste output. By tracking materials and processes closely, manufacturers can identify inefficiencies and implement waste reduction strategies. This approach supports sustainable production practices and lowers operational costs, as less waste means reduced material expenses. Companies can reuse or redirect materials to other areas within the production cycle, further promoting a circular economy.
Moreover, smart factories contribute to sustainability by reducing production’s carbon footprint. With AI optimizing logistics and supply chains, transportation routes and delivery schedules can be streamlined, cutting down on emissions associated with shipping and handling. As sustainability increasingly influences consumer choices, companies adopting smart factories can reduce their environmental impact and appeal to eco-conscious customers.
The Role of AI and Machine Learning in Quality Control
AI and machine learning are pivotal in enhancing quality control within smart factories. Traditionally, quality control relied on manual inspections, which could be inconsistent and prone to human error. Today, AI-powered vision systems can inspect products with extraordinary precision, detecting defects at every production stage. This ensures that only high-quality products reach the market, boosting consumer confidence and reducing the costs associated with returns or repairs.
Machine learning also enables these quality control systems to learn and adapt over time, improving their accuracy and efficiency. For instance, as the system encounters more defects, it becomes better at identifying subtle imperfections, ensuring higher quality standards. AI-driven quality control is invaluable in industries like pharmaceuticals or aerospace, where quality is paramount. Moreover, automated inspections can occur continuously without interrupting production, ensuring quality control does not become a bottleneck.
The Future of Smart Factories and the Global Manufacturing Landscape
In the years to come, as technology advances, smart factories will likely integrate even more sophisticated capabilities, such as augmented reality for training and blockchain for supply chain transparency. These developments will further enhance the adaptability and resilience of manufacturing systems. Adopting smart factories marks a new era in production—one where automation, sustainability, and human expertise come together to create a more efficient, responsive, and forward-looking manufacturing industry.